The Benefits Of Temperature Mapping With Data Loggers
Data loggers for warehouse temperature mapping.
In this article, we cover the following topics:
- When Are Data Loggers For Warehouse Temperature Mapping Needed?
- What Are The Benefits Of Using Data Loggers For Warehouse Temperature Mapping?
- How Can Adapt Ideations Assist With The Use Of Data Loggers For Warehouse Temperature Mapping?
How Can Data Loggers For Warehouse Temperature Mapping Be Useful?
The process of temperature mapping is imperative in understanding the climate within a cold storage warehousing facility, as this determines that goods have remained within correct conditions outlined. Warehouse temperature mapping can be concisely characterised as a thermally active snapshot of the current status within a cooling unit.
Cold storage facilities are often quite vast spaces filled with shelves used to hold goods that are temperature-sensitive for example before or after they have been manufactured or distributed. This paired with factors such as external weather, multiple entry points and constant movement of people within a warehouse, can heavily influence small to rapid changes in temperature within a controlled environment.
Goods kept in cold storage units are generally temperature-sensitive in nature or can be affected by humidity levels. This commonly includes products from specific industry sectors including biopharmaceuticals, perishable foods & beverages, and other cold chain related items.
How Does Data Loggers & Temperature Mapping Correlate?
In order to track any change in the climate of a cold storage facility and undergo the warehouse temperature mapping process, specific technology must be utilised, especially for goods that must be stored under such strict criteria. A common solution that has the capability to undergo such a task are known as data loggers. Essentially used as a near real-time temperature monitor, data loggers are often lightweight & durable devices, often connected to a user portal that can be used to access relevant data. In most cases they have the ability to gather a number of vital metrics such as temperature, location, light and shock depending on their capabilities and assist in tracking metrics such as OTIF performance.
When Are Data Loggers For Warehouse Temperature Mapping Needed?
Warehouse temperature mapping is a process that must be completed every 3 months to a year, though the regularity can change depending on factors such as protocols in place and the type of goods being stored. This task is repeated so frequently so that companies ensure they follow proper regulatory processes which in turn instils trust in their clients and ensures that all goods in storage remain within correct conditions. The process of temperature warehouse mapping takes a minimum of 24 hours with constant monitoring required.
In short, this important practice begins with selecting a data logger that will match a company’s specific needs. Locating areas of risk around a storage facility is the next step, followed by stationing the devices in those areas. The test is then run, where the devices are monitored closely and all data loggers being utilised for the test must display the same temperature within a certain range. For example, many vaccines must be stored between 2-8°C to avoid spoilage or loss of efficacy. This helps to gain an understanding of temperature fluctuations in different pockets of a warehouse. Once the test results are recorded, analysed, and changes implemented, the entire warehouse temperature mapping process is repeated with modifications until a stable storage environment in successfully achieved.
What Are The Benefits Of Using Data Loggers For Warehouse Temperature Mapping?
There is a plethora of benefits to utilising data loggers for warehouse temperature mapping. A few common benefits include:
- Continued awareness and control over warehouse climate: Especially when it comes to storing perishable goods such as meats and produce, it is important to ensure that the goods are being stored in an environment that meets
health and safety guidelines to avoid spoilage of products and to minimise the risk of negatively impacting consumer health.
- Preserving safety and minimising wastage: By understanding and maintaining an evenly distributed temperature throughout the cold storage facility with the help of data logging devices, it is easier to ensure biopharmaceuticals remain compliant. For example, if biopharma products do not remain within correct conditions this can lead to loss of efficacy or product damage. As a result of minimising wastage, it also means that deliveries will be fulfilled on time and product shortages or delays will be less frequent in relation to temperature excursions within cold storage facilities.
- Reliability of storage and data accessibility: Completing frequent warehouse temperature mapping helps instil confidence in the client that their goods will remain within the correct conditions outlined. They are also able to build a stronger relationship with the business as clients can also access the data gathered by the devices through a user portal if required. This helps to create increased transparency and therefore positively impact long standing business agreements.
How Can Adapt Ideations Assist With The Use Of Data Loggers For Warehouse Temperature Mapping?
Data loggers are an imperative part of the warehouse temperature mapping process. They are able to track specific temperature in different areas within a warehouse, ensuring that the overall climate remains balanced and goods in storage are being kept with the utmost care. Here at Adapt Ideations we have created unique and innovative data logging solutions that can be utilised for warehouse temperature mapping. We offer three main product ranges, namely KELVIN, PIXEL & PROTON.
Though all products within these ranges are extremely versatile, the PIXEL range is best suited to provide temperature and humidity data for cold storage facilities. PIXEL is a near real-time temperature data logger that has the ability to monitor temperature of cold storage facilities. PIXEL W100 can monitor humidity and temperature between -30°C to 60°C. PIXEL W300 is probe version of the solution with the ability to monitor temperature between -100°C to +100°C. The PIXEL Suite Of Devices are a simple yet powerful solution to your cold storage monitoring and warehouse temperature mapping needs.
Enquire to find out more about our innovative solutions and how they can be utilised at enquiries@adaptideations.com
Share Our Post.
Awards & Recognition

Best Temperature Monitoring Solution Provider
Awarded by India Biologics & Vaccines Outstanding Industry Awards 2022
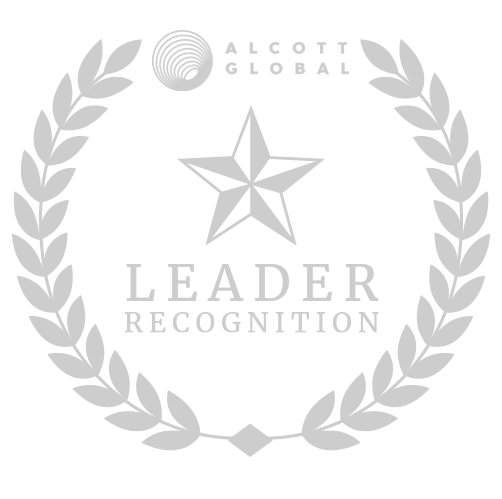
Adapt Ideations Recognised As A Supply Chain Leader
by Alcott Global on Supplify's Supply Chain Tech Map 2.0
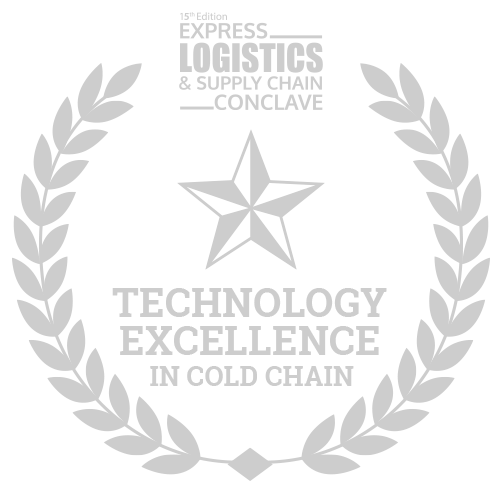
Related Articles.
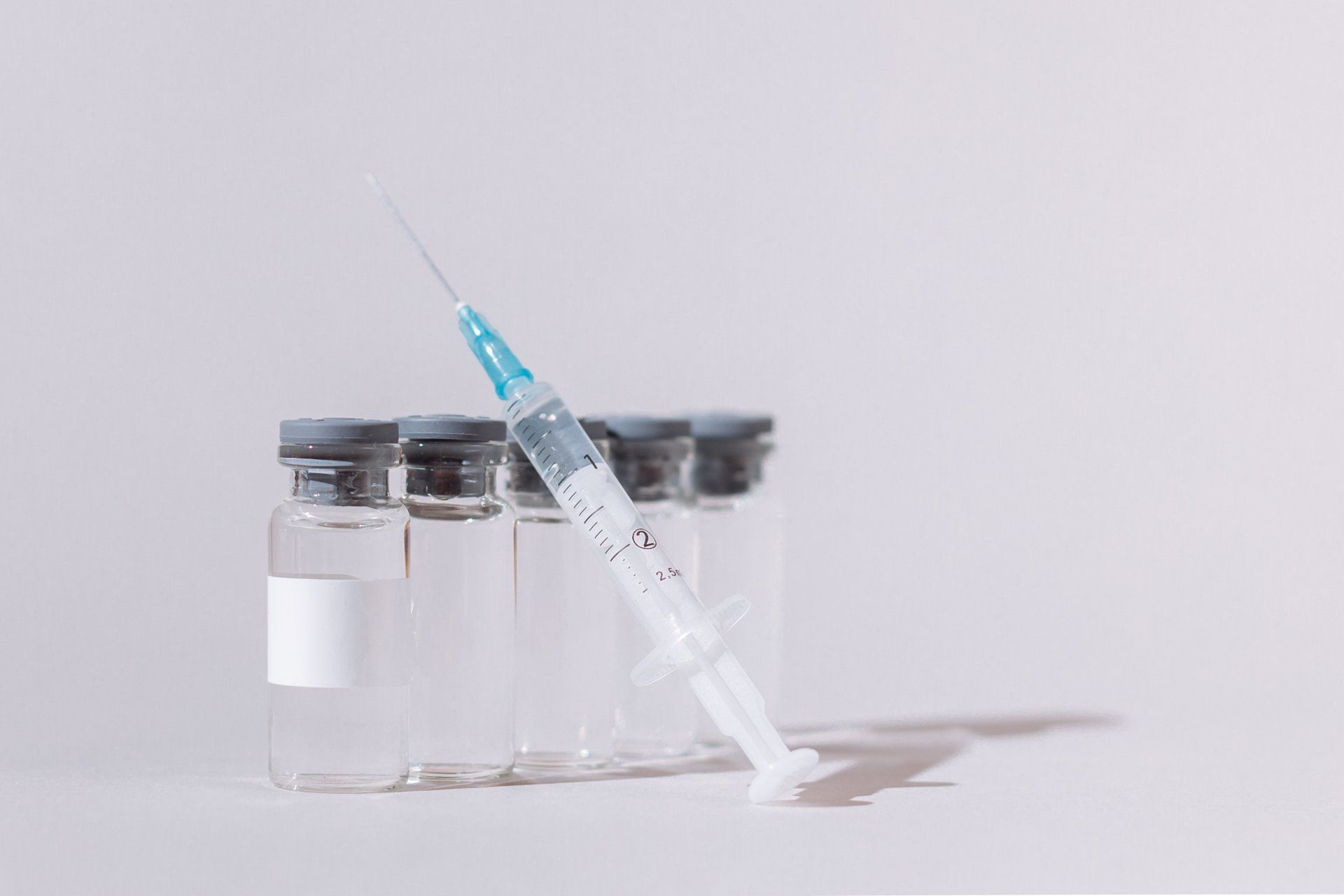
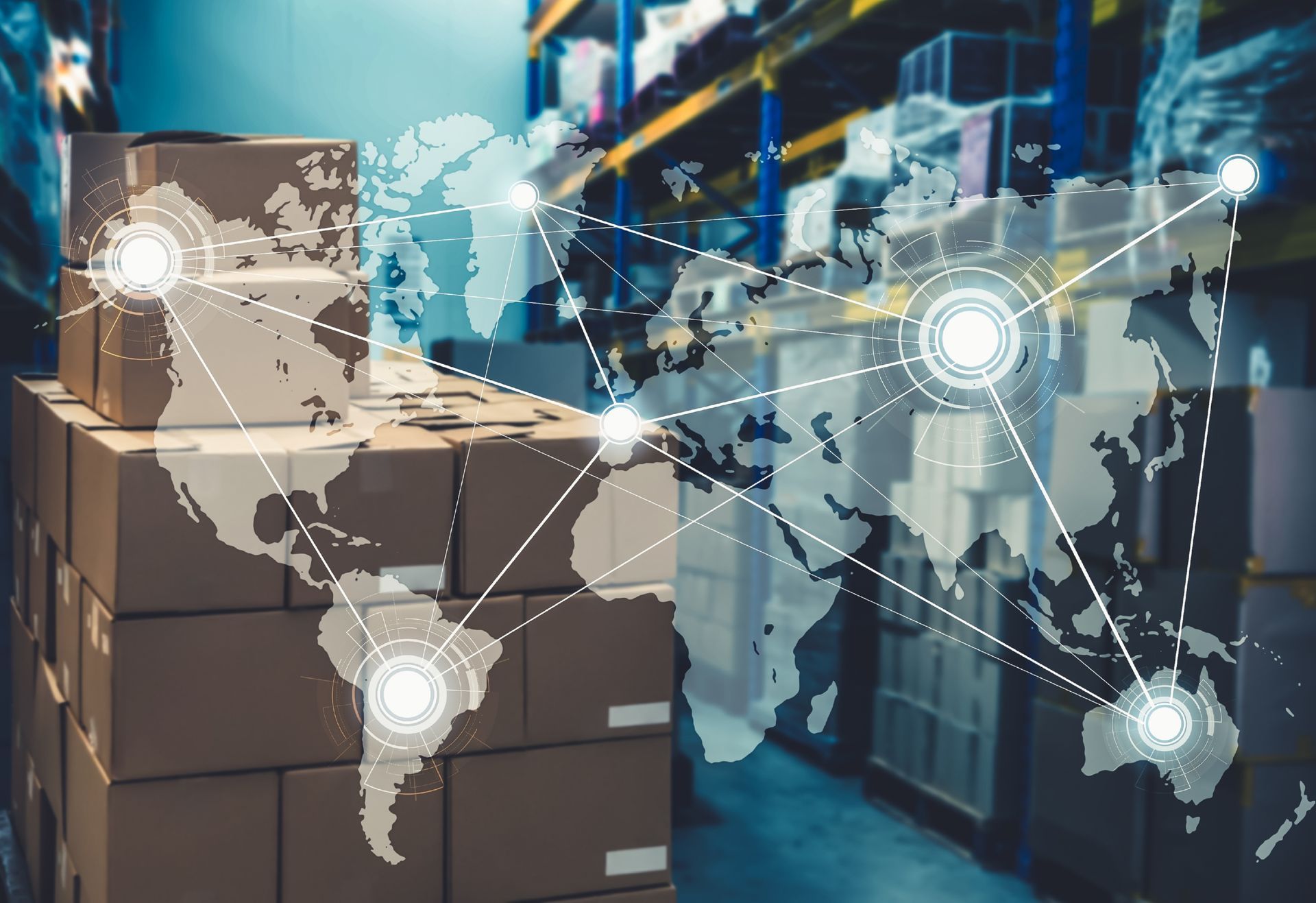
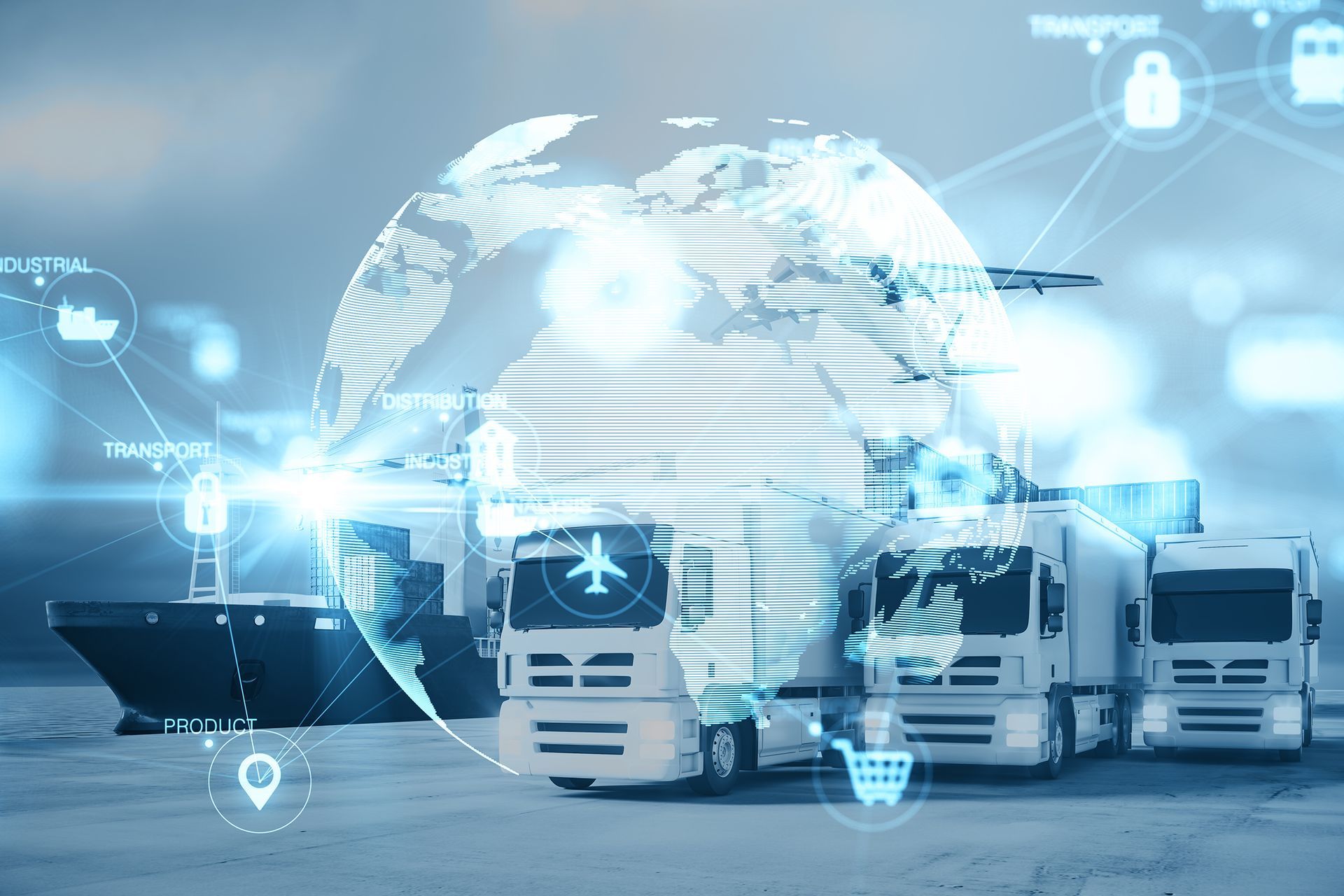