OTIF In The Supply Chain - What is it and how to calculate it.
OTIF In The Supply Chain.
In a supply chain setting, OTIF stands for "On Time In Full." It is a metric that is used to measure the success of a company's delivery process. OTIF can be calculated by measuring the number of deliveries made on time and in full by the total number deliveries. It can be used as a performance indicator for suppliers, manufacturers, and logistics companies. In this post, we will explain what OTIF is, how to calculate it and how it can help you maximise efficiency within the supply chain!
In this article, we cover the following topics:
- What is OTIF and what does it stand for?
- How OTIF is calculated
- Uses of OTIF in the supply chain
- Benefits of OTIF
- Challenges to achieving OTIF
- Tips for improving OTIF performance
What is On Time And In Full (OTIF)?
OTIF is a metric used to measure the success of a company's delivery process. OTIF calculates the percentage of on-time deliveries made in full vs. the total amount of deliveries and can be used as a performance indicator for suppliers, manufacturers, and logistics companies. Achieving OTIF in the supply chain can be challenging, but there are some tips and tricks that can help improve your OTIF performance.
Being on-time and in full (OTIF) has become increasingly essential for many logistics providers and within supply chains over the past few years, with big firms leading the way. In some instances companies that produce physical goods—in sectors such as food and beverages or consumer packaged goods—can be fined heavily if they don't meet OTIF KPIs.
OTIF is significant for businesses and CPG firms because it indicates that the product is available on the shelf when consumers are ready to buy. With the rise of products and SKUs, supply chain complexity is also increasing. However, this presents a lot of opportunity for value in the supply chain if it can be unlocked. This is easier said than done for a number of reasons.
OTIF follows the same basic steps as RTLS, but with some notable differences. First, because OTIF is a process that involves numerous parties (a merchant, a vendor, and a transporter), the problem gets more difficult as most organizations rely on their ERP systems to compute it. Because ERP typically does not have access beyond the "four walls" of the organization, trading partners may find it challenging to work together in order to optimize OTIF with legacy systems.
A large challenge of OTIF is consolidating data from your transportation partner into one place and ensuring its quality and consistency. Once you do so, platforms like Adapt Ideations' can help you monitor the data to assess performance over time, identify bottlenecks slowing your progress, and issues that are preventing you from meeting customers' expectations.
So, How Is OTIF Calculated?
OTIF is a supply chain and logistics industry acronym that refers to a metric that assesses a supplier's capacity to meet delivery deadlines and ensure the full quantity has been delivered to the correct location.
OTIF is composed of two distinct metrics:
On-Time
- (Delivery Time) - (Confirmed delivery time)
On-time tracking measures how close a delivery was to the scheduled appointment time.
In-Full
- (Cases matching the criteria) / (Total number of cases)
In-full is a term used to describe the quantity of product delivered to customers, relative to their request. In other words, it measures if customers have recieved more than they ordered, less than ordered or the correct amount that needs to be fulfilled.
What is the OTIF Formula?
The calculation of your OTIF rate is straightforward. It involves counting the total number of deliveries that were delivered on time and completely, and dividing that figure by the total number of deliveries. The following equation can be used:
On-Time In-Full Rate = Total deliveries made on time and in full / Total deliveries made X 100
We'll use a hypothetical example to explain the process in further detail. Assume you have 1200 orders and that 925 of them were delivered on time and completely. This indicates your On-Time In-Full rate would be:
On-Time In-Full Rate = 925/1200 X 100 = 77%
While a 100% OTIF rate is next to impossible, an accepted standard rate for eCommerce businesses for example is between 80- 90%. However, it's important to realize that different product lines may have diverse target scores.
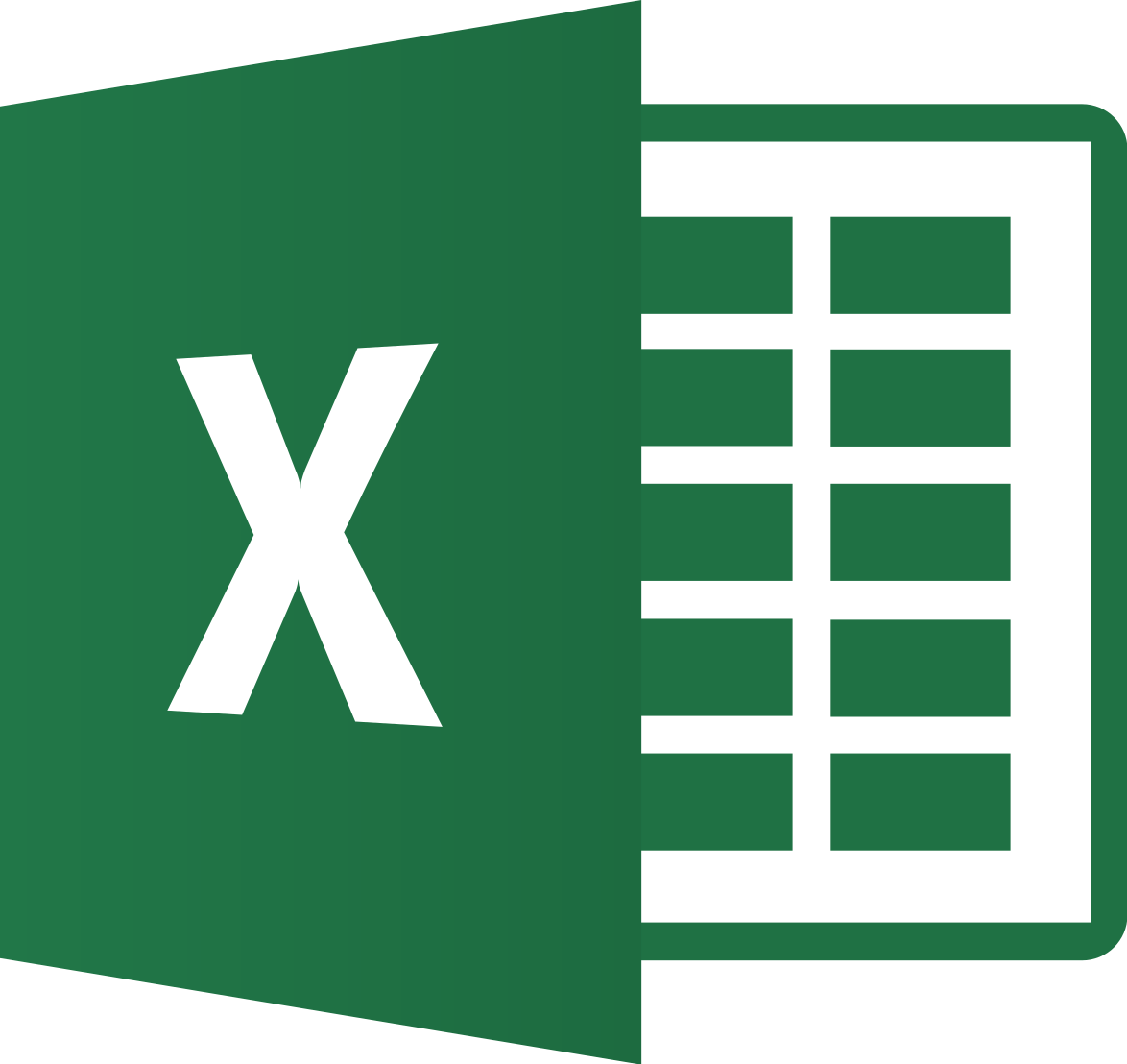
What is the OTIF Excel percentage formula?
The OTIF (On Time In Full) or DIFOT (Delivery In Full, On Time) excel percentage formula is calculated by taking the amount of deliveries made on time in full and dividing it by the number of all deliveries made. This formula, also known as the "on time delivery performance measurement", is commonly expressed as a percentage, which can be calculated using the basic formula =part/total
How to calculate OTIF in excel:
To calculate the OTIF (On Time In Full) percentage in Excel, you will need to know the number of deliveries made on time in full and the total number of deliveries made.
Assuming that you have this data in two separate cells, you can use the following formula:
- In one cell, enter the number of deliveries made on time in full (e.g., A1).
- In another cell, enter the total number of deliveries made (e.g., B1).
- In a third cell, enter the following formula:
=(A1/B1)*100
This formula will divide the number of on-time, in-full deliveries (A1) by the total number of deliveries (B1), and then multiply the result by 100 to express it as a calculating percentage. The result will be the OTIF percentage.
For example, if you have 90 on-time, in-full deliveries out of a total of 100 deliveries, the formula would look like this in Excel:
= (90/100) * 100
The result would be 90%, indicating that 90% of your deliveries were on time and in full.
OTIF in the supply chain.
For supply chains OTIF is a metric used to measure the success of a company's delivery process calculated by the number of deliveries made that are in full and on time against the total amount of deliveries made. This is a common tool used to understand the performance of various stakeholders within a supply chain such as suppliers, manufacturers, and logistics companies. Here are some of the ways OTIF can be used in the supply chain.
OTIF can be used to:
- Evaluate supplier performance
- Measure the effectiveness of manufacturing and logistics processes
- Identify potential bottlenecks in the supply chain
- Improve customer satisfaction
In some circumstances when companies fail to meet a retailer's on-time, in-full delivery requirements, they are fined. For example, some companies, like Walmart, fine shippers that don't deliver on time by 3% of the cost of the goods sold for each instance. When deliveries are not OTIF this can result in companies additional financial expenditure due to upfront costs for missing deliveries in addition to possibly losing sales opportunities.
Customer OTIF laws may differ significantly depending on how a business accounts for them. Being late for a delivery is only one of the circumstances that might result in hefty OTIF penalties. This can also have similar affects when deliveries are made earlier than expected.
The rising number of penalties reflects the necessity for shippers to have accurate, real-time information about the status and location of their products and assets. This is where real-time supply chain visibility comes in: By helping you see exactly where your shipments are at any given moment, it can help ensure timely arrivals and avoid costly delays.
Benefits of OTIF.
There are a number of benefits to using OTIF as a metric for success within the supply chain. OTIF can help companies identify and resolve potential bottlenecks in the supply chain, improve customer satisfaction, and measure the effectiveness of manufacturing and logistics processes.
Reduced shipping costs
OTIF helps businesses optimize their delivery process and reduce the cost of shipping. By reducing the number of late deliveries, businesses can save money on expedited shipping fees.
Improved customer satisfaction
OTIF helps businesses improve customer satisfaction by providing them with accurate information about the status of their orders. In addition, OTIF can help reduce confusion and missed deliveries.
Increased profits
OTIF helps businesses improve their bottom line by optimizing their delivery process. By reducing the number of late deliveries, businesses can save money on expedited shipping fees and improve customer satisfaction. All of these factors combined can lead to increased profits for a company.
OTIF can also be used to evaluate the performance of company's suppliers ensuring contractual agreements are complied with. When suppliers deliver products on time and in full, it can help reduce the risk of stockouts and improve customer satisfaction. Overall, OTIF is a valuable metric that can help companies optimize their delivery process and improve their bottom line.
Challenges to achieving OTIF.
Despite the benefits of OTIF, achieving it can be challenging. Many factors can impact on-time delivery, including weather conditions, traffic congestion, mechanical failure and warehouse damages. Often shipping and receiving deadlines can be tight, making it difficult to meet OTIF requirements particularly if delivery windows are missed.
Another challenge to OTIF is each customer often has different expectations and requirements for when deliveries need to be received. Some customers are willing to receive their orders early, while others expect them to arrive on time or only accept late deliveries as a last resort. This makes it difficult for companies to establish standardized OTIF targets across all product lines.
Finally, meeting OTIF requirements can be expensive for businesses. Fines for missed deliveries can add up quickly, and investing in technologies that improve supply chain visibility can be costly. However, the benefits of OTIF outweigh the costs in most cases.
Tips for improving OTIF performance
There are a number of things businesses can do to improve their OTIF performance. Some of the most effective tips include:
1 - Establish standardized OTIF targets across all product lines.
This will help ensure that all products are held to the same delivery standards.
2 - Implementing a warehouse management system.
The best warehouse management system will make it easier to keep track of your inventory and streamline the handling process. It lets you maintain track of your inventory levels and connects with your ecommerce site to ensure that stock levels are updated in real-time. This improves order accuracy by decreasing mistakes that may occur by managing processes manually resulting in greater efficiency. Furthermore, improved visibility into where specific SKUs are stored may reduce pick times and improve order completion rates.
3 - Use real-time supply chain visibility to track the status and location of shipments.
With near real-time supply chain visibility, businesses can track the status and location of their shipments. This information can help identify potential delays and prevent costly missed deliveries. In addition, real-time supply chain visibility can help improve customer satisfaction by providing them with accurate information about the status of their orders.
4. Communicate with suppliers and customers about OTIF expectations.
This will help reduce confusion and ensure that everyone is aware of delivery timelines.
5. Manage inventory levels carefully to avoid stockouts.
This will help keep deliveries on schedule and avoid late penalties.
In order to improve OTIF performance, businesses should establish standardized OTIF targets across all product lines, use real-time supply chain visibility to track the status and location of shipments, invest in technologies that improve supply chain visibility, communicate with suppliers and customers about OTIF expectations, and manage inventory levels carefully. By following these tips, businesses can optimize their delivery process and improve their bottom line.
Technologies that improve supply chain visibility.
In order to improve OTIF performance, businesses should invest in technologies that improve their supply chain visibility. Technologies that can help improve OTIF include warehouse management systems, transportation management systems, and asset tracking and monitoring solutions.
Warehouse management systems (WMS)
Warehouse management systems (WMS) help businesses track their inventory and optimize the handling process. A WMS can connect with an eCommerce site to update stock levels in real-time, which reduces order inaccuracies and speeds up the delivery process. In addition, a WMS can help businesses identify and resolve potential bottlenecks in the supply chain.
Transportation management systems (TMS)
Transportation management systems (TMS) help businesses plan, manage and optimize their transportation resources. A TMS can connect with other systems within the company to ensure that all aspects of the delivery process are working together efficiently. This can help reduce the risk of stockouts and improve customer satisfaction.
Asset Tracking & Monitoring Solutions
Asset tracking and monitoring solutions like Adapt Ideations innovative solutions provides businesses with vital information on metrics associated with their shipments. This information can help identify violations of set parameters allowing delays and further challenges to be reduced. In addition, the ability to share data with other stakeholders within the supply chain assists in breaking down silos and creates greater transparency.
All of these technologies can help businesses improve OTIF performance and optimize their delivery process.
OTFI Frequently Asked Questions
Conclusion.
There are many benefits to achieving OTIF performance. For suppliers, it can help reduce the risk of stockouts and improve customer satisfaction. For manufacturers, it can help optimize the delivery process and improve bottom line results. And for logistics companies, it can help increase efficiency and reduce costs.
However, there are also several challenges that businesses face in trying to achieve OTIF performance. These challenges include establishing standardized OTIF targets across all product lines, using real-time supply chain visibility to track the status and location of shipments, communicating with suppliers and customers about OTIF expectations, and managing inventory levels carefully.
By following these tips, businesses can optimize their delivery process and improve their bottom line.
Enquire to find out more about our innovative solutions and how they can be utilised at enquiries@adaptideations.com
Share Our Post.
Awards & Recognition

Best Temperature Monitoring Solution Provider
Awarded by India Biologics & Vaccines Outstanding Industry Awards 2022
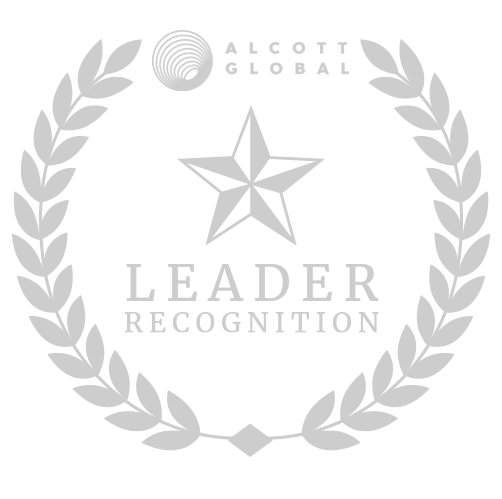
Adapt Ideations Recognised As A Supply Chain Leader
by Alcott Global on Supplify's Supply Chain Tech Map 2.0
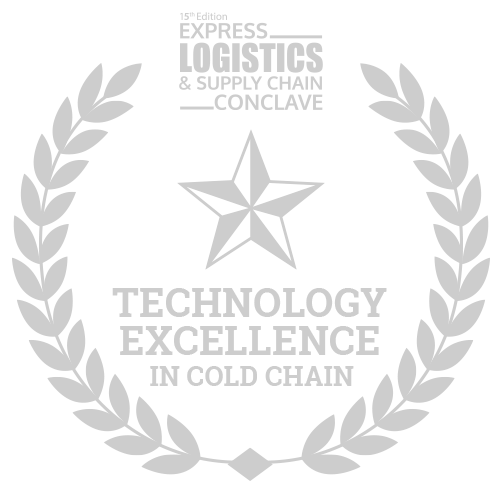
Related Articles.
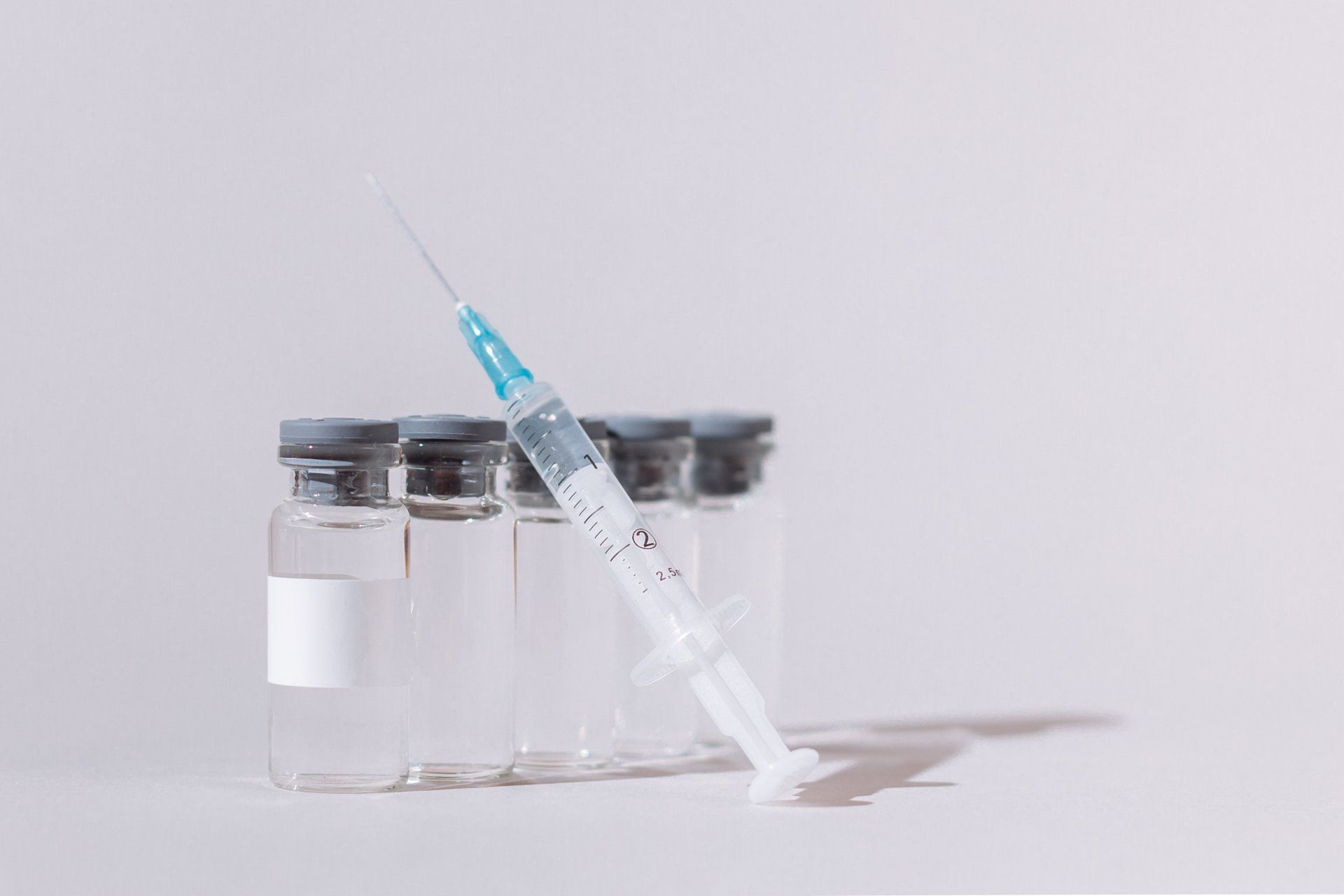
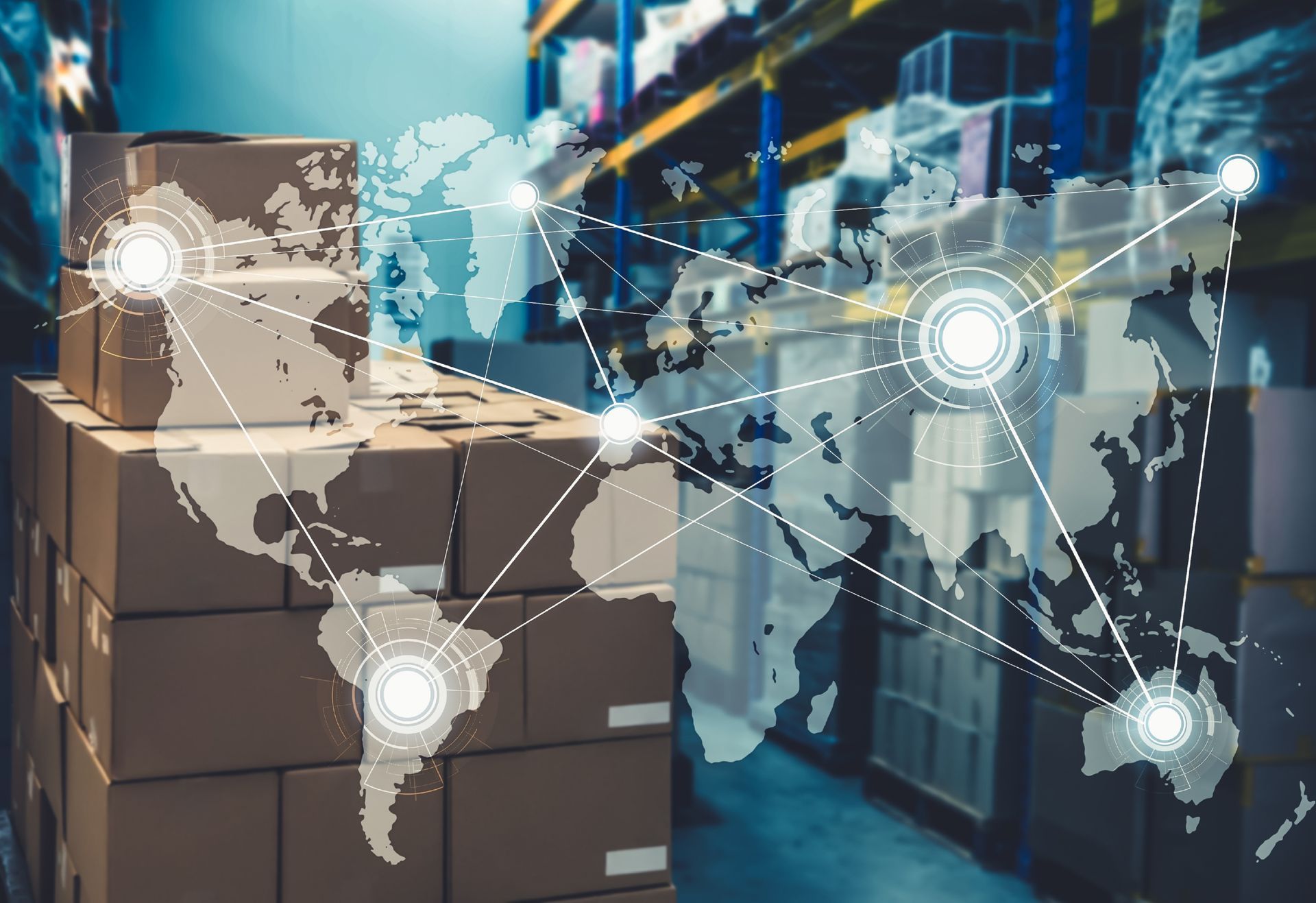
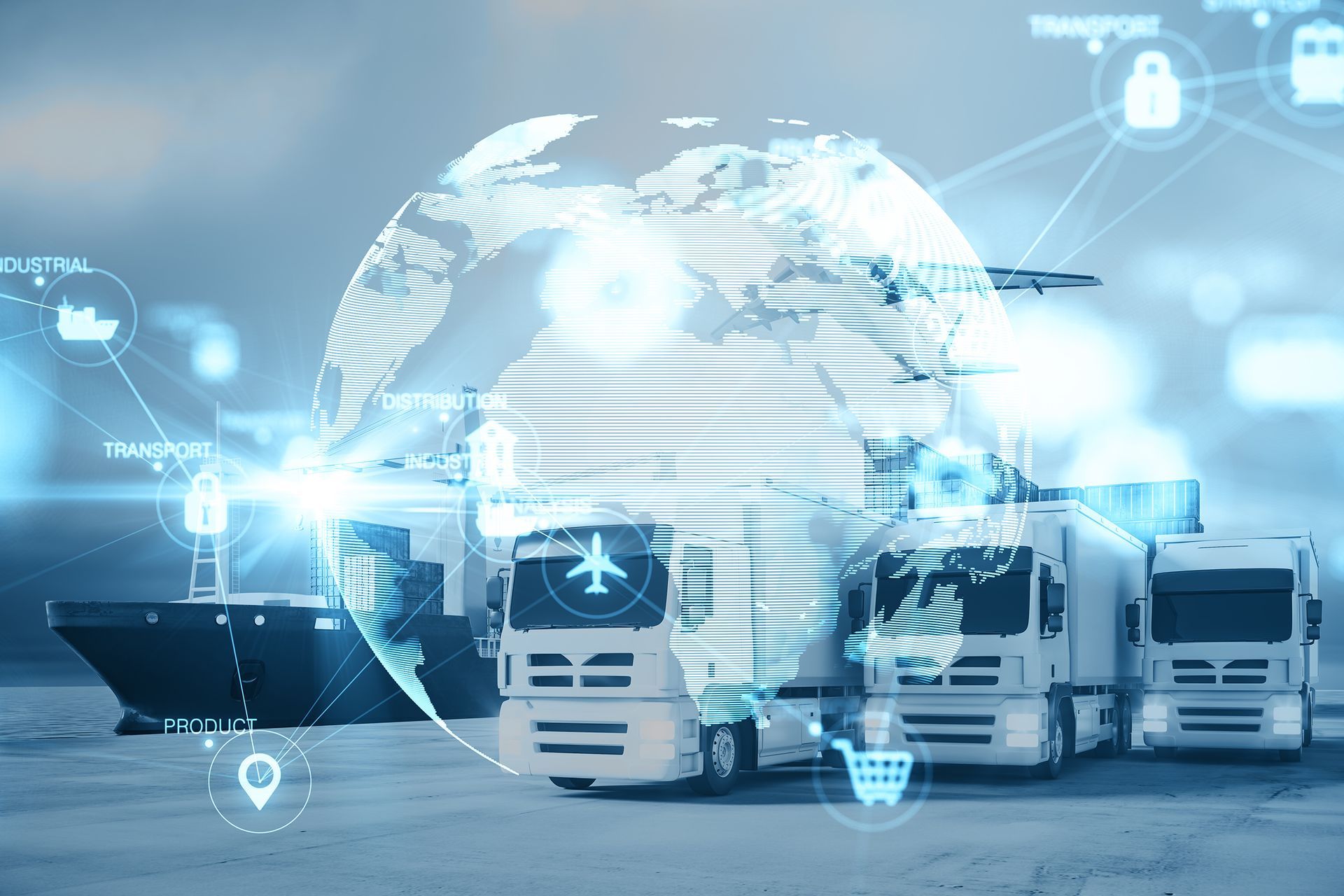