Can Cold Chain Operations Be Optimised With Data Analytics?
In the intricate web of global supply chains, where temperature-sensitive products journey from one corner of the world to another, the significance of cold chain operations cannot be overstated. Whether a product is a pharmaceutical or perishable food, maintaining precise temperature control is critical for ensuring quality and safety. Companies around the world are finding cold chain management challenging due to the complexity of supply chain networks and strict quality standards introduced by relevant authorities. Now is the time for data analytics to emerge as a beacon of hope offering the potential to revolutionise cold chain operations.
Understanding Cold Chain Operations
Cold chain operations involve a series of precisely controlled stages, each crucial to maintaining the product's integrity. Yet, ensuring the right temperature conditions from start to finish is no simple task. With around 20% of drugs wasted due to cold chain malfunctions, and the food industry witnessing even more significant losses, it's evident that precise temperature control is essential.
Read more about - Chilling Success: Mastering Cold Chain Logistics.
The Role Of Data Analytics In Cold Chain Optimisation
A. Enhancing Efficiency Through Data-Driven Insights
Data analytics emerges as a game-changer in this complex landscape. By analysing real-time data, organisations gain actionable insights to improve their processes continuously.
Imagine a scenario where a temperature fluctuation during transit triggers an immediate alert. Such timely information allows quick corrective actions, preventing a potential disaster.
Case in point: A leading pharmaceutical company managed to reduce cold chain disruptions by 30% after implementing data analytics. Real-time insights and immediate corrective actions led to this impressive improvement.
Look out for our PIXEL and KELVIN suites of devices if you're looking for real-time monitoring solutions that will alert you when temperature fluctuations happen.
B. Demand Forecasting & Inventory Management
Accurate demand forecasting is essential for eliminating overstocking or understocking issues. Data analytics mines historical data, market trends, and external factors, providing refined demand predictions. The optimisation process leads to companies saving money and reducing waste.
Case in point: A food-market giant in the United States used data analytics to predict seasonal demand variations accurately, leading to a 15% reduction in food wastage. Efficient inventory management based on these insights also resulted in significant cost savings.
C. Supplier Performance & Quality Control
Monitoring suppliers in real-time ensures adherence to quality standards. Data analytics helps identify potential issues early, enabling companies to address delays or deviations before they escalate. Also, you can attain more visibility by integrating data from temperature data loggers and sensors, and quality control is able to reach new heights.
To assist you in this Adapt Ideations’ IoT-enabled temperature data logger solutions can be a great help. Submit your details today to
book a discovery call.
Real-Time Monitoring & Temperature Data Loggers
In the realm of cold chain management, real-time monitoring is a game-changer. With the help of temperature data loggers, businesses obtain precise and continuous temperature data.
These loggers serve as vigilant sentinels, sending immediate alerts in case of temperature fluctuations. Swift corrective actions can then be taken, minimising product damage and loss.
This technology provides invaluable insights enabling stakeholders the power to detect temperature fluctuations instantly. Consider the scenario of a seafood exporter using temperature data loggers to detect a refrigeration malfunction, preventing a potential disaster in the form of spoiled seafood. This can be easily monitored with automated monitoring solutions such as Adapt Ideations’ PIXEL devices.
Way Forward
In the pulse of every cold chain operation lies the heartbeat of data analytics. It steers the course of efficiency, sustainability, and product integrity. From pinpointing inefficiencies in cold chain operations to foreseeing demand. It's the driving force of optimisation.
Cold chain operations aren't just about preserving goods. They're about maintaining trust, reputation, and lives. Data analytics is the compass that ensures these operations navigate smoothly, delivering on their promise with accuracy and precision.
As you dive into the depths of cold chain operations, consider the possibilities that data analytics brings. Explore the resources, tools, and technologies that can lead your business to a new era of efficiency. Discover the magic of real-time monitoring and temperature data loggers, ensuring your products reach their destination unscathed. Enquire today to take the first step to join the movement towards data-driven cold chain optimisation.
Common FAQ's
Get in touch with us today at enquiries@adaptideations.com for further information on our solutions.
Share Our Post.
Awards & Recognition

Best Temperature Monitoring Solution Provider
Awarded by India Biologics & Vaccines Outstanding Industry Awards 2022
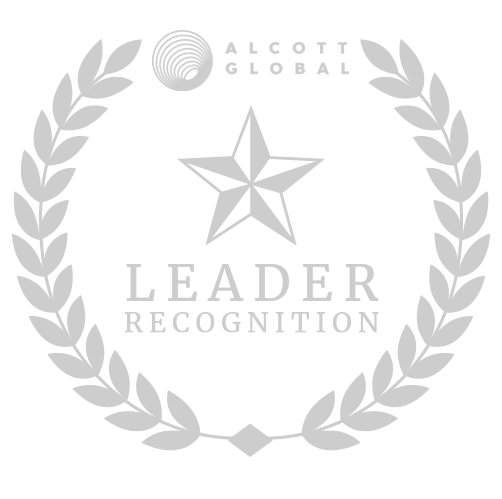
Adapt Ideations Recognised As A Supply Chain Leader
by Alcott Global on Supplify's Supply Chain Tech Map 2.0
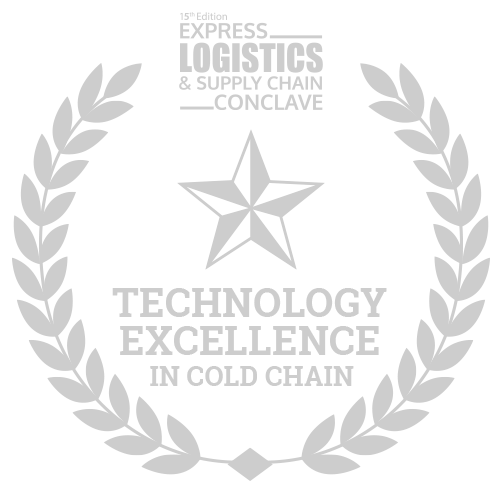
Related Articles.
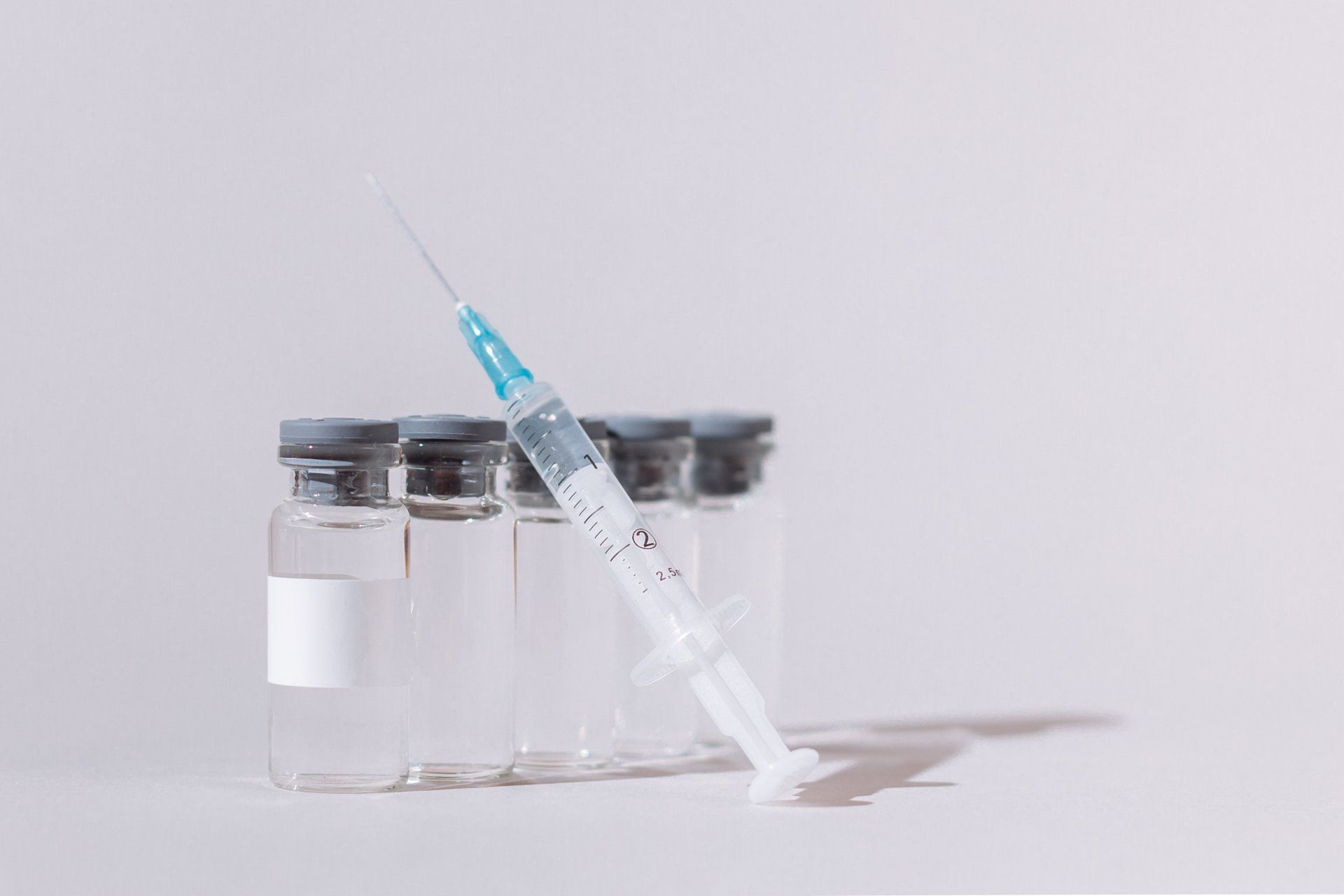
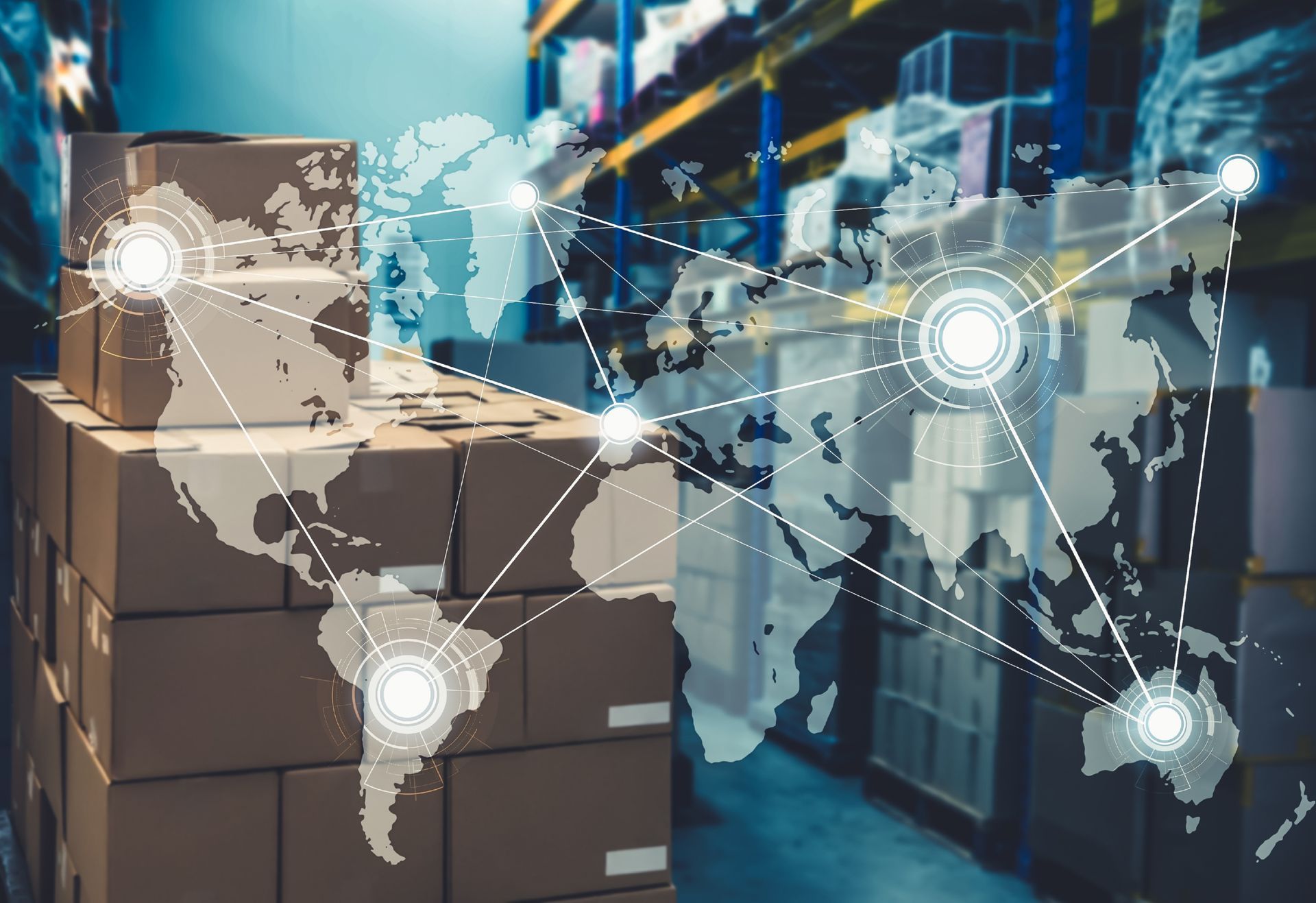
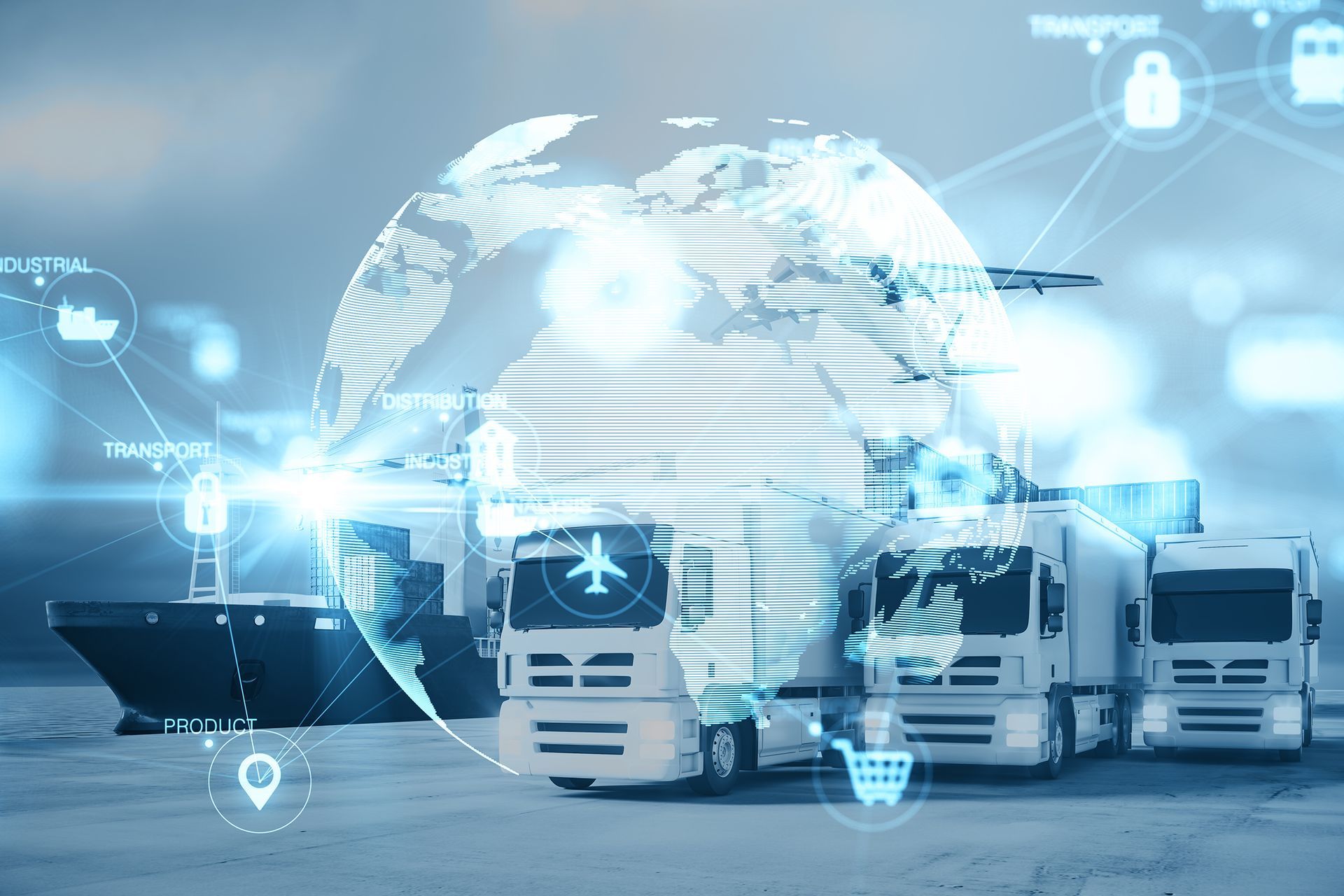